Precision sheet metal fabrication processes offer a highly versatile and efficient way to manufacture a wide array of OEM components and products. Many companies opt to utilize contract sheet metal fabricators — like EVS Metal — as it allows them to leverage specialized expertise and streamline their production processes. If you’re considering working with a fabrication company, it’s natural to have questions about how this type of metal fab works. In this comprehensive guide, we will address these questions, and provide insights to help you make a well-informed decision.
Understanding Contract Sheet Metal Fabrication
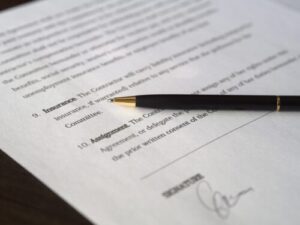
Contract sheet metal fabrication involves outsourcing the production of sheet metal components or products to a specialized manufacturer. The fabrication company works under a contract, delivering the specified products based on the customer’s requirements. This allows businesses to leverage the expertise and capabilities of the fabrication company for efficient and precise production.
Materials Used in Sheet Metal Fabrication
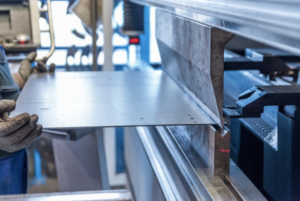
Sheet metal fabrication involves the use of various materials, each with unique properties and applications. Here are some commonly used materials:
- Steel: Carbon steel, stainless steel, and galvanized steel are popular choices due to their strength, durability, and corrosion resistance. Carbon steel is versatile for general applications, stainless steel offers superior corrosion resistance, and galvanized steel provides protection against rust.
- Aluminum: Known for its lightweight nature and excellent corrosion resistance, aluminum is extensively utilized in industries such as aerospace, automotive, and electronics. It can be easily shaped and possesses good conductivity.
- Copper and Brass: These materials are valued for their excellent electrical conductivity and thermal properties, making them ideal for electrical and heat transfer applications. Copper is commonly found in electrical wiring and conductors, while brass is favored for decorative and architectural purposes.
- Titanium: Renowned for its high strength-to-weight ratio, exceptional corrosion resistance, and biocompatibility, titanium finds applications in industries such as aerospace, medical, and chemical processing. It is particularly well-suited for environments with high temperatures or aggressive chemicals.
- Nickel Alloys: Offering outstanding resistance to heat, corrosion, and oxidation, nickel alloys are frequently employed in demanding environments like chemical processing, power generation, and oil and gas industries. They are highly regarded for their strength and thermal stability.
Types of Products Manufactured Using Precision Sheet Metal Fabrication Processes
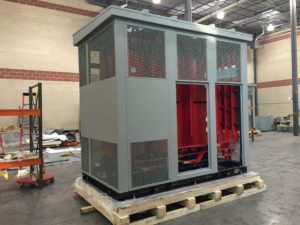
Sheet metal fabrication offers immense versatility, allowing for the production of a wide range of products. Here are some common examples:
- Enclosures and Cabinets: Sheet metal is used to create durable enclosures and cabinets for electronics, telecommunications, and industrial equipment. These structures provide protection, electromagnetic shielding, and a visually appealing appearance.
- HVAC Components: Sheet metal fabrication is commonly employed in the production of air ducts, vents, and other heating, ventilation, and air conditioning (HVAC) components. These elements ensure proper airflow, temperature control, and efficient ventilation in commercial and residential buildings.
- Automotive Parts: The manufacturing of automotive parts heavily relies on sheet metal fabrication. Body panels, fenders, brackets, and exhaust systems are crafted with precision forming, welding, and surface finishing techniques. These components must meet stringent industry standards and withstand challenging operating conditions.
- Electrical Enclosures and Panels: Sheet metal is utilized to manufacture enclosures and panels for electrical distribution, control systems, and power generation equipment. These enclosures provide protection against electrical hazards, house delicate components, and facilitate organized wiring and circuitry.
- Aerospace Components: Sheet metal fabrication plays a critical role in the aerospace industry, producing aircraft components such as wings, fuselage parts, engine enclosures, and structural frames. These components necessitate the use of lightweight materials, precise machining, and strict quality control measures to comply with aerospace regulations.
- Kitchen Equipment: Sheet metal fabrication finds extensive application in the production of kitchen appliances and equipment, including sinks, countertops, cabinets, range hoods, and food preparation surfaces. Stainless steel, known for its hygiene, durability, and ease of maintenance, is a popular choice in this domain.
- Industrial Machinery Parts: Sheet metal components are vital for machinery used in manufacturing processes, construction, and other industrial applications. Brackets, frames, guards, and equipment housings are meticulously fabricated to ensure precise fit and proper functioning within these systems.
Benefits of Contract Sheet Metal Fabrication
Collaborating with a fabrication company for sheet metal production offers numerous advantages that contribute to the success of your business:
Access to Specialized Equipment and Expertise
Fabrication companies are equipped with cutting-edge machinery, such as CNC machines, laser cutters, and press brakes, that enable precise and efficient production. They possess specialized knowledge and skills, staying abreast of industry trends and technological advancements, ensuring optimal results.
Cost Savings
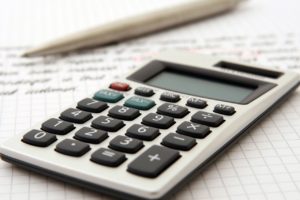
Outsourcing sheet metal fabrication proves to be a cost-effective solution compared to establishing in-house manufacturing facilities. By partnering with a fabrication company, you eliminate the need for significant investments in expensive equipment, specialized personnel training, and the maintenance of production infrastructure.
Efficient and Timely Production
Fabrication companies have extensive experience in streamlining production processes, resulting in efficient workflows and timely delivery of finished products. Whether you require large volumes or complex projects, they possess the expertise to handle them with precision and efficiency.
Scalability
Fabrication companies offer the flexibility to meet varying production needs. Whether you require a small batch or a large order, they can readily adjust their production capacity to accommodate fluctuations in demand. This scalability ensures that your requirements are met without compromising on quality or delivery timelines.
Quality Control and Assurance
Established fabrication companies prioritize quality control to ensure that the products meet your specifications and industry standards. They employ dedicated quality assurance teams and adhere to rigorous inspection protocols. Additionally, certifications such as ISO 9001 demonstrate their commitment to delivering high-quality products consistently.
Design Flexibility and Customization
Fabrication companies provide valuable design assistance and customization options based on your specific requirements. Their experienced engineers and designers offer insights to optimize your product designs for manufacturability and functionality, resulting in enhanced end products.
Streamlined Supply Chain Management
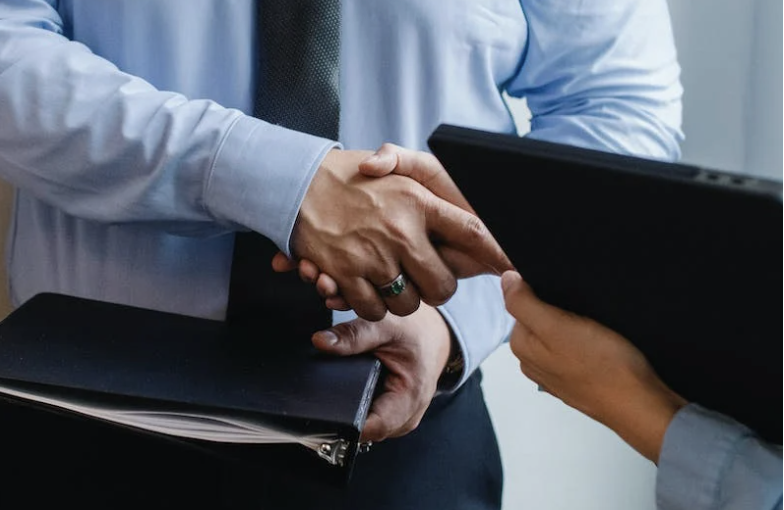
Outsourcing sheet metal fabrication simplifies your supply chain. You no longer need to worry about raw material sourcing, equipment maintenance, or labor management. Fabrication companies have established relationships with material suppliers, ensuring a steady supply of high-quality materials, streamlining your production process.
By partnering with a reliable fabrication company, you can leverage their specialized equipment, expertise, and streamlined processes to achieve cost savings, efficient production, superior quality control, design flexibility, and a simplified supply chain. These benefits empower your business to thrive in the competitive sheet metal fabrication industry.
The Fabrication Process
The sheet metal fabrication process involves several key steps to transform raw materials into finished products. Let’s explore each step in more detail:
Design and Specification
Customers provide drawings, specifications, or CAD files outlining their requirements. Collaborating with the fabrication company’s design team helps optimize the design for manufacturability and cost-effectiveness. This step ensures that the final product meets the customer’s expectations and can be efficiently produced.
Material Selection
The appropriate sheet metal material is chosen based on the desired properties and specifications. The fabrication company provides guidance on material options, considering factors such as strength, corrosion resistance, conductivity, and aesthetics. Selecting the right material ensures that the final product possesses the necessary characteristics.
Cutting
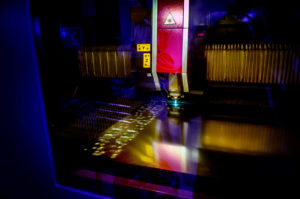
Metal sheets are cut to size using techniques like laser cutting. These methods ensure precise and clean cuts, maintaining the integrity of the material. Accurate cutting is crucial to achieving the desired dimensions and ensuring the proper fit of the components.
Shaping and Forming
Metal sheets are shaped through processes such as bending, rolling, stamping, or deep drawing. CNC press brakes, roll forming machines, and stamping presses are commonly used to achieve the desired shapes and dimensions. Shaping and forming techniques give the sheet metal its intended structure and geometry.
Joining
Components are joined together using techniques like welding, riveting, fastening, or adhesive bonding. Welding is a common method for creating strong and durable connections, while riveting and fastening provide flexibility for disassembly or repairs. The joining process ensures that the individual parts come together to form a cohesive and functional product.
Surface Finishing
Surface treatments like painting, powder coating, plating, or anodizing are applied for improved aesthetics, durability, or corrosion resistance. These finishes enhance the appearance, protect against environmental factors, and ensure longevity. Surface finishing not only adds a visually appealing touch but also enhances the product’s performance and lifespan.
Inspection and Testing (QA/QC)
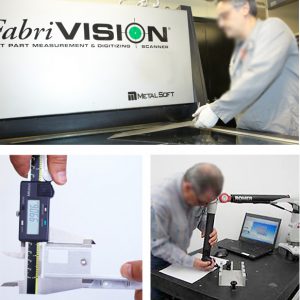
Finished products undergo inspections and tests to ensure they meet quality standards and specifications. This includes dimensional checks, visual inspections, hardness testing, and functional tests to verify performance. Thorough inspections and testing guarantee that the fabricated product meets the required quality criteria.
Packaging and Delivery
Once approved, the products are appropriately packaged to ensure protection during transit. Fabrication companies work with shipping and logistics partners to arrange timely delivery to the customer’s specified location. Proper packaging safeguards the product from damage while transportation ensures the final product reaches the customer in a secure and efficient manner.
By following these detailed steps, the sheet metal fabrication process ensures high-quality products that meet customer requirements and industry standards.
Questions to Ask a Fabrication Company
When considering a potential fabrication partner, it’s important to gather detailed information. Here are some questions to ask:
Q: Do you provide design and engineering services, or do I need to provide my own designs?
- Understanding whether or not the fabrication company offers design and engineering support is crucial. Their expertise can optimize your product for manufacturing efficiency and potentially save costs.
Q: Can you accommodate custom requests and unique specifications?
- Ensure that the fabrication company has the capabilities and flexibility to handle custom projects. Discuss your specific requirements and confirm if they can meet them effectively.
Q: What certifications and qualifications do you hold?
- Inquire about the certifications and qualifications the fabrication company possesses. Certifications like ISO 9001 indicate their commitment to quality management systems. Depending on your industry, other relevant certifications may be significant as well.
Q: What are the shipping and logistics options for delivering finished products?
- Understanding the company’s shipping capabilities and logistics network is important for timely delivery. Discuss their shipping options, transit times, and packaging methods to ensure your products arrive safely and on schedule.
Q: Do you offer any warranties or guarantees on your work?
- Ask about warranties or guarantees provided by the fabrication company. This ensures that you have recourse if any issues arise with the finished product. Clarify the terms and conditions of any warranties to ensure customer satisfaction.
By asking these detailed questions, you can make an informed decision when selecting a fabrication company that aligns with your specific needs and requirements.
Contract sheet metal fabrication offers a cost-effective and efficient solution for producing high-quality components and products. By understanding the fabrication process, materials, benefits, and asking the right questions, you will be able to select a reliable and experienced fabricator who will be a valuable and trusted resource with which to partner for many years to come.